I Description
This line is digital control cut-to-length, servo motor feeding; By choosing CRGO strip shape on the touch screen and inputting dimension, the line will automatically punch and cut strips. There are “two punch + two cut” line and “one punch + two cut” line. Transformer lamination strip shapes can be as below:
II Main features
- Full automatically, from decoiling to stacking, only three operators are needed
- Good & reliable punching/shearing power: imported hydraulic servo control, quick speed, low noise and long life
- Good & reliable feeding power: big torque AC servo motor, quick responding, high positioning precision, low noise, low braking heat loss, long life
- Track positioning: servo motor pulling ball screw, linear guide positioning, quick, accurate, convenient; automatically memberizing track width.
- Movement control: adopts advance PCC controller, Ethernet Powerlink communication technology, massly reduces wire connection and so raise the reliability, stability and realtime ability of the system; remote control and diagnosis
- Simple & intuitive operation: choose strip shape and input sizes and dimensions on the touch screen
- Adopts inverted-support collecting method which can collect and order 5m long strips and reduces the vibration, thus reduces affects to magneting performance of CRGO strips during processing.
- Equipped with Step-Lap function, step-lap quantity can be 7.
- Imported world famous brand parts, such as linear rail, ball screw, bearings, etc., assure machine long life
- New improved COLUMN-STACKING function, five columns (two yokes, two side limbs and one center limb) can be stacked automatically. Stacking precision +/-0.3mm.
III Line buildup:
3.1 Double-head hydraulic expansion decoiler, inverter control, automatic decoiling
3.2 Automatic servo feeding system
3.3 Servo controlled O-shape punching press
3.4 V-shape punching press, servo controlled transverse feeding
3.5 45°electric shear, servo control, central positioning
3.6 135°electric shear, servo control, central positioning
3.7 Track positioning device
3.8 Flat belt transmitting device
3.9 Collecting system (servo positioning, magnet absorbing)
3.10 Double-layer unloading car
3.11 Electric control system, and control box
3.12 Pneumatic system
IV Main technical data:
Code
|
BHX-400
|
BHX-600
|
BHX-900
|
CRGO coil width
|
40-440mm
|
60-640mm
|
80-920mm
|
Cutting length
|
300-2500
|
400-3500
|
500-5000
|
CRGO thickness
|
0.23-0.35
|
0.23-0.35
|
0.23-0.35
|
Cut-to-length precision
|
±0.2mm
|
±0.2mm
|
±0.2mm
|
Burr height
|
≤0.02mm
|
≤0.02mm
|
≤0.02mm
|
Cutting angle precision
|
±0.025°
|
±0.025°
|
±0.025°
|
Feeding Speed
|
0-240m/min
|
0-240m/min
|
0-240m/min
|
One cut duration
|
≤230ms
|
≤240ms
|
≤250ms
|
Cutting tool life
|
1,200,000 times before grinding
|
Punching tool life
|
500,000 times before grinding
|
Max. step-lap stroke
|
25mm
|
25mm
|
25mm
|
Step-lap quantities
|
1, 2, 3, 4, 5, 6, 7
|
Positioning method
|
Central line positioning
|
Strip collecting method
|
Inverted support type, auto stacking
|
HMI
|
10.4'' VGA color TFT display and 44 function keys and 20 system keys
|
Total electric power
|
25kW
|
30kW
|
35kW
|
Line occupation (LxWxH)
|
15m×5m×2m
|
18m×5.5m×2.5m
|
22m×6m×2.5m
|
V Sample image on touch screen:
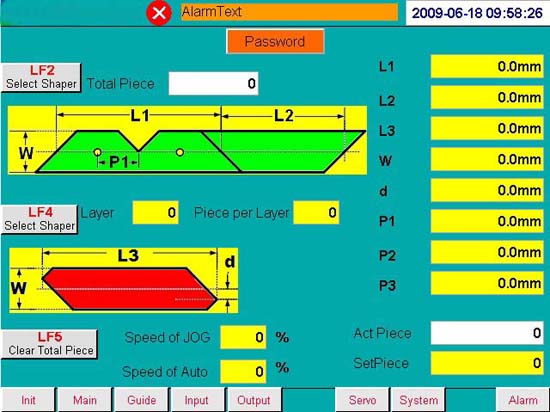
|CRGO cut-to-length line| CRGO cut-to-length line| CNC crgo cut-to-length line| automatic CRGO cut-to-length line|